从数字化、自动化走向智能化正泰新能向制造业高峰攀登
近年来,随着人工智能、工业互联网、大数据等信息技术的快速发展,光伏行业的数字化、智能化程度也越来越高。2022年初,工业和信息化部等五部门曾联合印发《智能光伏产业创新发展行动计划》,提出建设智能光伏产业生态体系的目标。从中国制造到“中国智造”,光伏行业业已迈入智慧光伏时代。
正泰新能一直是“中国智造”的先行者和实践者。早在2016年,正泰新能就建成全球首家“光伏制造+互联网”透明工厂,并获评“中德智能光伏示范基地”。其后,引进先进自动化生产线、自主研发MES系统、行业首家引入EL瑕疵AI自动检测……正泰新能在智能制造的探索从未止步,不断拓展技术边界,引领光伏行业向更数字化、智能化方向发展。
01 会“思考”的工厂:行业首家引入EL瑕疵AI自动检测
在光伏电池与组件的工序流程中,几乎每个关键环节都伴随着质量检测工序,确保生产过程中每个环节的高品质。以组件生产流程为例,从最初电池片的串焊、叠焊,到叠层、层压后的半成品,再到完成接线盒安装、装框、固化等流程后的成品,质量检测贯穿从电池片到最终组件成品始终。部分关键环节的检测,往往还包含对外观、内部缺陷检测两个部分。
在AI检测尚未大规模应用之前,检测工序通常以人工目检的方式实现,耗时长、占用人工多、成本高,因而行业内往往采用人工抽检的方式,不仅低效,还常有漏网之鱼出现,影响产品质量保障。而AI智能检测的出现,为光伏检测工序提供了更具效率和精确度的有力工具。
AI智能检测,简单来说,就是将一块电池、组件放到与计算机相连接的摄像头下进行拍摄,让计算机通过图像进行检测分析,以此识别产品是否存在缺陷。正泰新能于2018年与阿里云合作,借助工业大脑AI图像质检技术,在行业内首次引入EL瑕疵AI自动检测,并成功应用到正泰新能的所有基地车间中。
AI智能检测基于人工智能深度学习算法搭建,集算法集成、模型训练、模型部署和检测输出于一体,能智能识别并判定电池组件常见的缺陷类型。光伏行业中的AI检测通常可分为:外观AI检测、EL AI检测,两者可以简单理解为对电池组件的外部、内部缺陷分别进行检测的技术。
外观AI检测是针对电池组件外观的智能检测,能精准识别异物、焊带移位、气泡等8种常见瑕疵,检测半成品是否符合设定标准等。此外,外观AI检测在识别组件片间距以及爬电距离方面拥有人类无法匹敌的“火眼金睛”,几乎可以做到零漏检。
EL AI检测、外观AI检测上线后,不仅显著提升产品检测的质量、水平和效率,还极大节省了人力成本。以半成品AI检测工序为例,往常两条产线白夜班需8个人配合共同完成,而AI检测上线后,仅需2人即可,瑕疵识别率较人工提升了6.48%。
AI检测,加上AOI检测等智能检测手段的运用,让正泰新能电池组件产线的智能检测覆盖率大幅提升,人工抽检被机器全检所替代,关键工序均实现了百分百在线全检,产品出厂合格率得到极大提升。此外,与行业内不少企业采购第三方AI设备不同,正泰新能拥有独立的AI智能运维技术团队,可自主运维保障AI检测稳定高效运行,给客户提供高水准的产品质量体验。
目前,正泰新能电池在线智能检测覆盖率达72%,准确率达98%+。组件端包括串检、半成品、成品、灌胶、边框、盒盖、铭牌等智能检测工序在内,智能检验覆盖率达92%,准确率直击99.7%,成为业内为数不多智能检验覆盖率超90%的企业之一。
02 数智化工厂:条形码背后的全生命周期追溯
如果留意,正泰新能出品的每一块光伏组件都能看到一个条形码,它相当于组件的身份证,是这一片组件终身唯一可识别的编码。
从生产开始,这个编号就被激光注入,在进入每一道工序前,在线扫码枪对其进行自动扫描。与此同时,正泰自主研发的MES根据工单预先设定好的物料信息,调整对应工艺参数,选择对应原材料投入生产。后续组件生产的每一道工序,都将在工单设定好的路径下进行。产品出厂后,用户可通过扫描该产品唯一对应的条形码,追溯该产品从原料到工艺、设备,再到出厂时间、配置参数等全流程信息,实现全生命周期可追溯。
在这一智能化生产流程中, MES、SPC、质检App等质量管控工具都在协同发挥作用,共同助力工厂智能化制造管理系统的实现。其中,MES,也即制造执行系统的作用尤其显著。MES系统通过采集不同客户的不同要求,在制造流程中对工艺路径、参数、条码等信息进行在线相互验证。一旦出现异常或超出预设,MES将暂停工序并进行追踪监控,同时将情况实时反馈到系统看板中,让管理者第一时间掌握动态。
而SPC,联合质检app,又能通过采集、记录每日关键过程数据,对过程能力进行分析,提前管控风险,保障了整个生产过程的稳定。
一块条形码带来的高度集成信息背后,是数控化制造装备、智能化制造管理系统、云端大数据应用等高新技术的综合呈现,也是正泰新能工厂从数字化、自动化走向智能化的一个缩影。
03 全自动工厂:AGV无人驾驶小车助力
不同于组件车间的全流水线操作,光伏电池车间的工序流程更具独立性,前后工序之间并非从一个机台流转到下一个机台,而是需要在一道工序结束后,将电池片码堆缓存,再搬运到下一道工序中,这就意味着大量的物料搬运需求。
在传统车间,生产制造的机器设备往往数控化程度高,但物料搬运环节并没有更好的解决方案,尽管低效,往往还是通过人力搬运来实现。为了有效提高物料搬运效率,降低劳力成本,正泰新能于2022年在电池车间引入AGV智能小车,实现了全车间搬运的自动化。
如今正泰新能的电池车间里,到处可见AGV小车来回穿梭,看上去比一线车间工人还要忙碌。装满电池片或空车前行的AGV,按照设定的行驶路径移动,遇到人或其他障碍物,AGV配备的高精度激光避障传感器将发挥作用,进行减速并发出预警,保障人车安全。
为满足日产数百万片电池片的运输配送要求,海宁基地共配备有226辆AGV无人驾驶小车,匹配有93个自动充电桩,所有小车通过中央管理系统进行全数字管理调度。中央管理系统通过匹配前后工序的搬运需求,自动调度AGV执行搬运任务,小车从任务位置接取硅片后,运输硅片到下一工序进行制程工艺。整个过程中央系统可全程监控,AGV的运送覆盖电池车间中从发料、制绒、硼扩,到LPVCD、去PSG、丝网印刷、包装等各个环节,实现物料的全自动补给及配送。
伴随AGV小车的导入,海宁车间生产人员缩减40%,极大节省了人力。同时,自动充电的配置让AGV可以24小时连续运转,大大提高了搬运效率,助力电池车间全自动化的实现。
处于快速发展中的光伏行业,无论在制造端还是应用端,都在加快与新一代信息技术融合的步伐,不断提高智能化程度,让更具精确度、更高品质和更高效率的光伏产品成为可能。保持创新是光伏企业在技术快速迭代更新的洪流中立于不败之地的保证,未来正泰新能将紧跟技术前沿,以智能创新驱动行业持续健康发展,在致力于成为全球最具竞争力的光伏组件供应商的道路上不断前行。
郑重声明:此文内容为本网站转载企业宣传资讯,目的在于传播更多信息,与本站立场无关。仅供读者参考,并请自行核实相关内容。
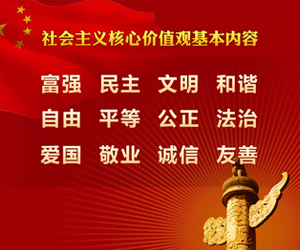